VAKOTA’s Matt Kocyba is currently working on an innovative residential project in Greenwich, Connecticut, with clients who share his passion for green living and sustainability. Our eco-friendly approach to the design is the number one priority throughout each decision-making process
Using – and reusing – water
During the initial planning stages of this sustainable, eco-friendly project, it took us roughly two years to go through the zoning department. This was down to the stipulations surrounding the wetlands in the grounds – and a lot of it related to the septic location.
In Greenwich – and in most coastal towns – it is required to manage your own water on your property. We were therefore required to set up a primary septic system, and a future secondary septic system design that works so that there is a backup if the primary setup should fail.
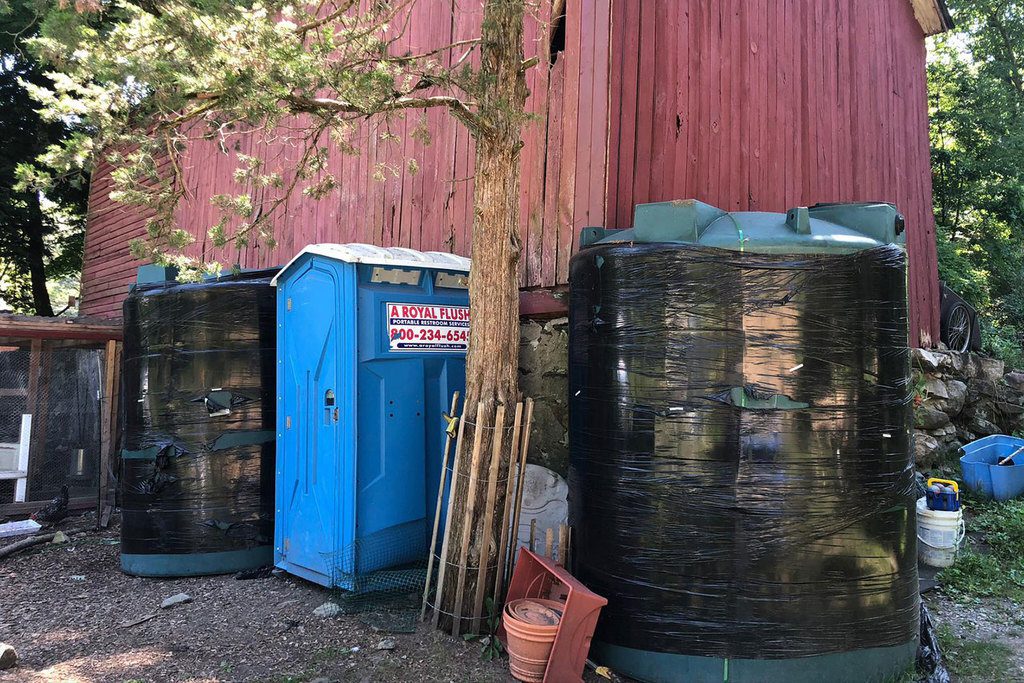
It took a lot of maneuvering to turn the house and garage to get this into place between the building setbacks, wetlands and septic clearance. When we eventually did get town approval and began to move forward, we had designed a rain garden in place of the traditional plastic septic tank. The rain garden is a much more eco-friendly option that can absorb drainage water efficiently and safely.
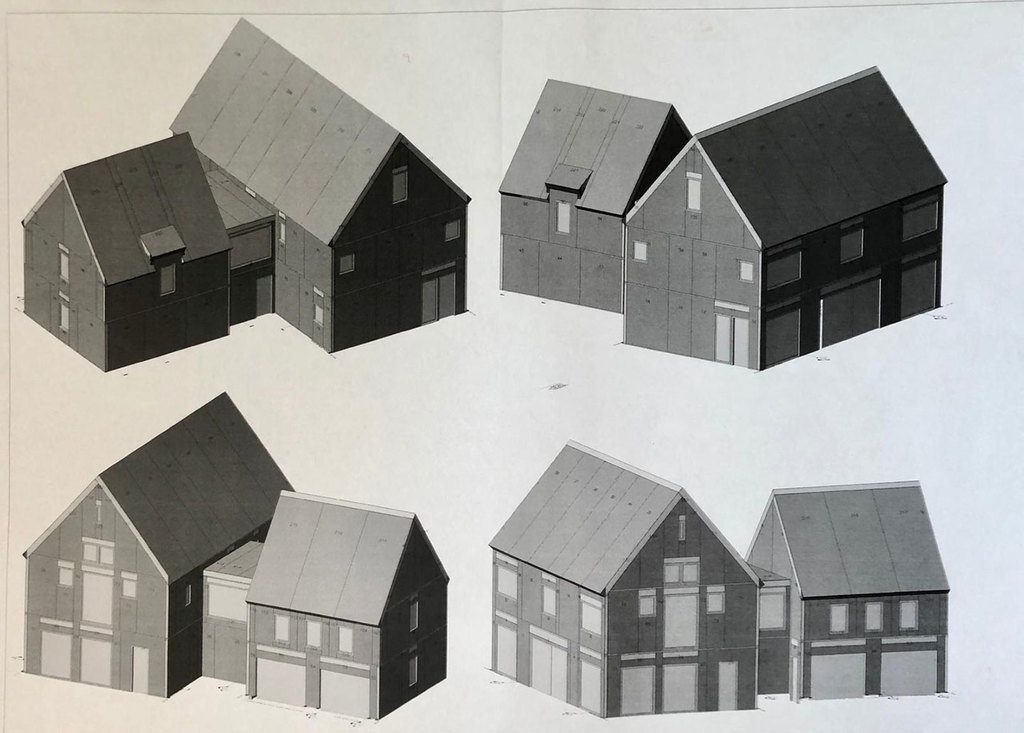
Drainage from the property, such as from the gutters, is now directed to two 6ft by 8ft high rainwater storage tanks – these can hold up to 1500 gallons each. These tanks are stored in a heated and conditioned storage room on the back side of the house, they are now set up for supplying filtered rainwater to the toilets and washing machine. Reusing water in such a direct way is highly beneficial for the environment as it takes away a lot of the need for external water supply.
We had hoped to go one step further and have a system for reusing Gray Water from the laundry system. Whilst, unfortunately, local regulations don’t allow for the reuse of Gray Water in residential properties in the state of Connecticut, we have put the necessary piping in place so that, in the event of a change in regulations, the client can hook into and begin to implement this quickly and easily.
As well as making the facilities as efficient as possible in their use of water, we also looked at alternatives to water altogether. One approach we have seen gain in popularity recently is the building of compostable toilets. Waste is treated as any other organic matter, composted and reused for fertilizer on the farm premises. Despite their increased popularity in recent years, we’ve yet to see one installed indoors.
We had planned to install the compostable toilet in the first-floor powder room. This involved backing the toilet to an outside wall so that it could be cleaned from the exterior. The design also required good ventilation, but as we got closer to the permit stage, we relocated the facility to the barn structure, to save on running plumbing to an additional area on the property.
Environmentally friendly finishes
“I learned sustainability, solar design and passive solar design at college,” Matt explains. “I went to a school in New Hampshire, that has an Eco-friendly mindset which is a part of the culture up there. I took that mindset and weaved it into my everyday life and profession. As architects, it is in our basic responsibility to design projects in the most efficient way with the least waste, best efficient layout and setup the structure in a way that best suits efficiency. A huge part of what makes it work well is pre-planning. You can control a lot of the sustainability aspects within the whole design – not just the aesthetic and architectural elements.”As a part of the pre-planning on this project, we focused on the products and finishes that would have a direct environmental impact.
Underneath the slab, we needed a good insulation that would not allow the radiant floor heating to seep into the ground. However, a lot of these foam insulations produce out-gassing. Matt specified a water-blown and low VOC insulation within the design to lessen the out-gassing.
The same issue can be said when it comes to paints and stain finishes. The floor stain that Matt chose for the house is Rubio Monocoat – an oil based stain that is known for its no VOC. Whilst oil based stains are known to be more toxic than water based stains, they are far more effective at penetrating and enriching the grain of the wood – so selecting an oil based stain that has no VOCs and reduces environmental impact is a major advantage when looking to keep projects sustainable and eco-friendly.
“I always spec the Rubio Monocoat,” Matt explains. “But sometimes the client’s budget doesn’t allow for it. We’ve been so lucky with the client on this project – as they’re so passionate about keeping the project as environmentally friendly as possible, it makes it a joy searching to find the best materials, when we have the same mindset, rather than struggling to convince the client to go in this direction.
“It really takes a team all working toward the same goal, some excellent planning and everyone in their specialty doing the best that they can to make a project like this as efficient as possible. I’m really proud of the work we’ve done on the Eco House. I look forward to more projects with such a heavy focus on sustainability and keeping the environmental impact in our thoughts always.”
Further Reading
Building an Eco-house: Part 1
Read more about our approach to choosing the right position and materials in Part 1 of this series
Building an Eco-house: Part 2
Read more about methods of heating/cooling the space, as well as the use of on-site materials in the build in Part 2 of this series