VAKOTA’s Matt Kocyba is currently working on an innovative residential project in Greenwich, Connecticut, with clients who are passionate about green living and sustainability. Our environmentally conscious approach to the design is our number one priority throughout each decision-making process.
– Read more about our approach to choosing the right position and materials in Part 1 of this series
Getting the right temperature
As mentioned in Part 1 of this series, we chose to use Structural Insulated Panels (SIPs) in the design and construction of the new house. One of the key benefits of this method of construction is the ability to seal the exterior envelope up tightly, with very little opportunity for infiltration of the elements – including hot or cold air temperatures.
Where a traditional house might ‘breathe’ through the wall, Eco House has panel construction that makes it possible for the occupants to completely control the inside environment. We are using a Mitsubishi mini-duct system to tie in with the Energy Recovery Ventilation (ERV) system, which will bring fresh air into the property via air ducts alongside the air conditioning and de- humidifier. Each aspect of the smart system works together to ensure proper air flow, that the humidity is comfortable and the air always fresh. With such a tightly sealed house, it is important to ensure the air inside doesn’t become stale or stagnant.
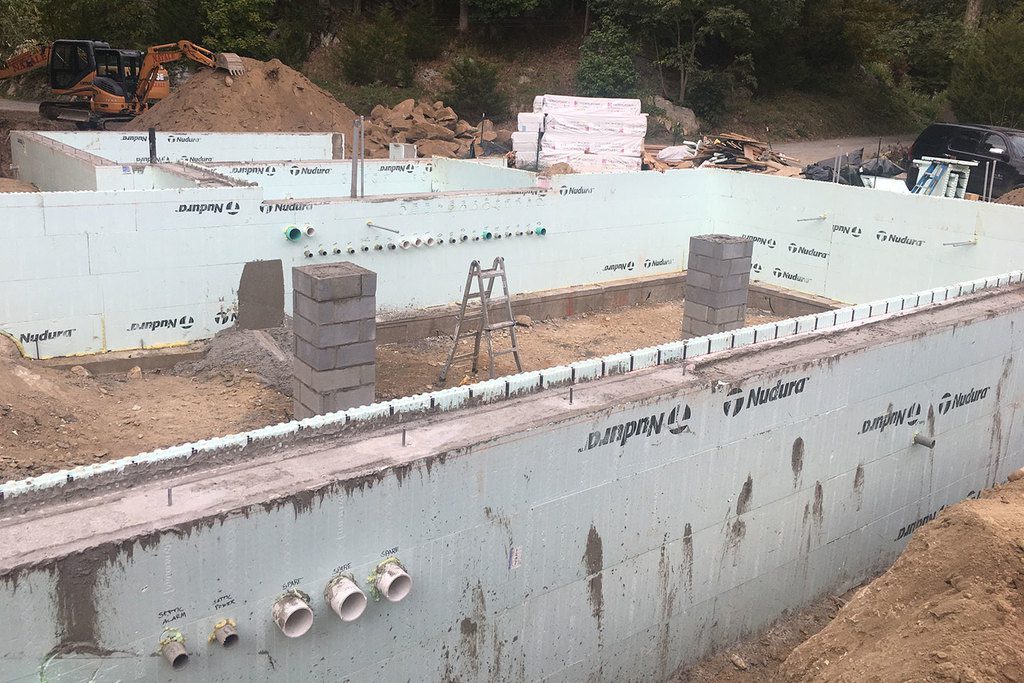
The heating we have chosen is radiant floor heating built into the floor slab. As with all our decisions on this project, we chose this approach with sustainability in mind. Radiant floor heating is a more economical method of space heating for several reasons.
Firstly, it puts the heat where you are! Heating that radiates from the floor upwards is most proficient at heating the first six feet of the space – typically where the people are. The room cools as it gets higher, which keeps heat circulating naturally through the room – unlike forced hot air, which can get dusty and difficult to get where you need it.
As it’s difficult to work with the directional nature of forced hot air, you can end up over-heating spaces and using far more energy than is necessary, just to get the warmth to where you are.
Plus, the mini-duct system can not only act as a cooling system via air conditioning, but also as a supplement to the heating system come winter.
The polished concrete slab also picks up passive solar heat from all the exposure with all the south facing glazing, which is particularly useful during cooler summer nights or in the autumn season when you don’t want to turn the whole radiant floor heat system on – the heat from the daytime is released via the thermal mass that is the floor slab, so your feet don’t get cold but no extra energy is needed.
As a result of all of the above steps, we should see that the house has no extreme spikes in temperature – even if any of the systems malfunction, the house is tight enough and the consistent ambient temperature in the house, there’s little need for drastic cooling or heating attempts, regardless of the weather outside.
Reusing materials
Our clients have been particularly vocal about their passion for sustainable materials – and we could not agree more.
“I always try to use the most economical and sustainable products possible in my designs – but these clients wanted to go further, and I was happy to oblige!” says Matt.
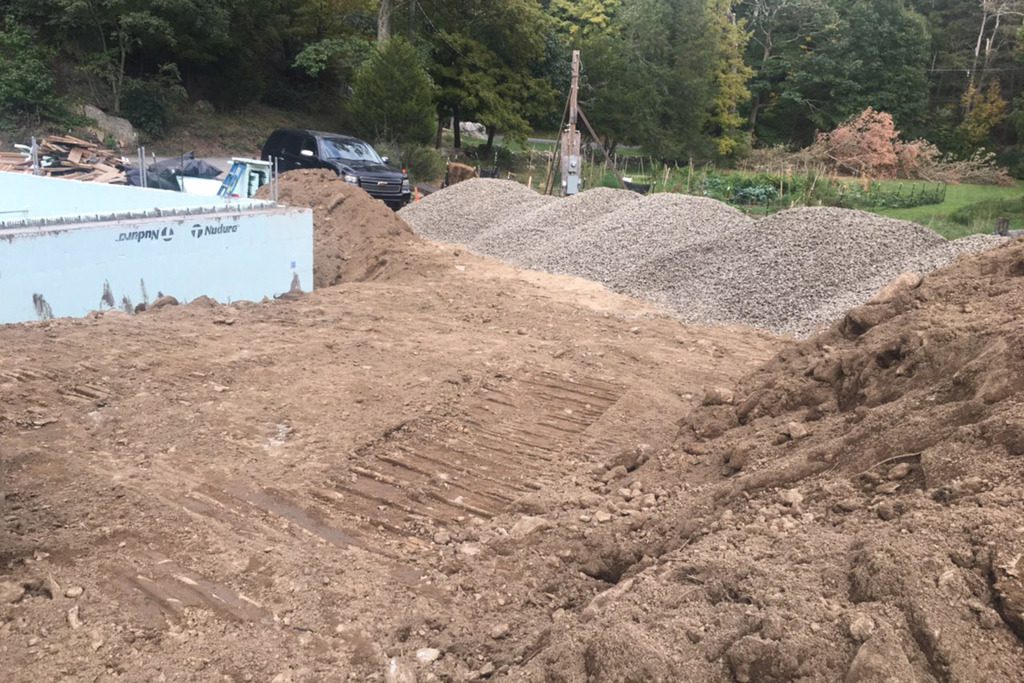
During the demolition of the original house, our clients asked that we keep as much waste material on-site as possible.
The original electrical cables came from overhead wires on the roadside. In Connecticut, there are often power outages when weather is bad, or trees come down over powerlines. However, to bring these cables underground, we needed to chop down an old spruce tree that was growing in the cables’ path.
We got the go-ahead to remove the tree – with the provision that we reuse it within the project. The clients had a dining room table created with the timber, leaving the live edge on display to represent the character of the tree. This is in storage, ready to bring back on-site once the house is complete.
We then created wooden beams with the remainder of the wood. The lower level of the house is designed as open-plan, and so the raw beams will be used decoratively, to delineate the living room and the foyer from the other open spaces.
As well as the spruce, we also had to remove some rock ledge during the demolition of the original house to make way for the new foundation. The clients requested that we keep and store all of the chipped away rock, in order to reuse the materials on-site.
The rock is now being kept for use in retaining walls, stone perimeter walls and even a stone terrace.
At VAKOTA, we always try to be eco-friendly with our designs – and so working on this project has been incredibly fulfilling for us. Finding creative ways to be energy conscious and to reuse the local materials, is not only pleasing our clients and creating a really great and low-impact house – it’s also been a great way to identify new sustainable techniques that we can take with us into new projects.
Part 3 of our Eco-House series looks at how we will be using (and reusing) water and guttering on the property, as well as the eco-friendly finishes we will be using.